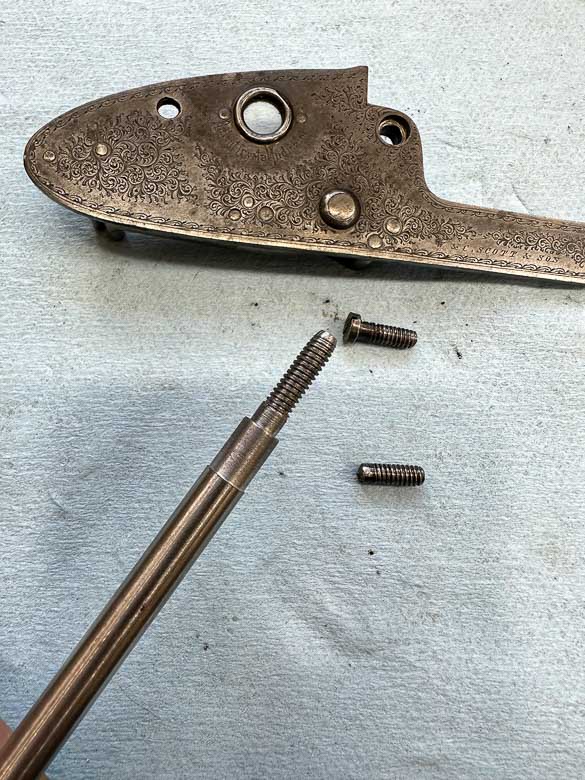
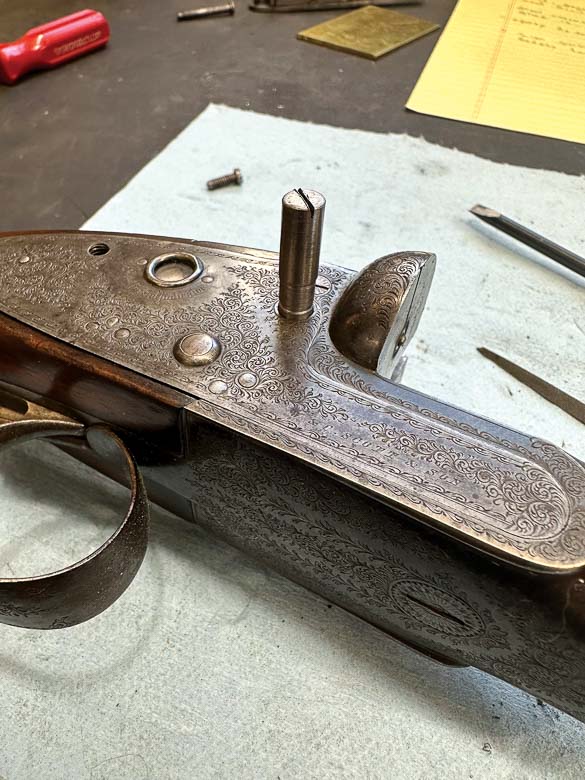
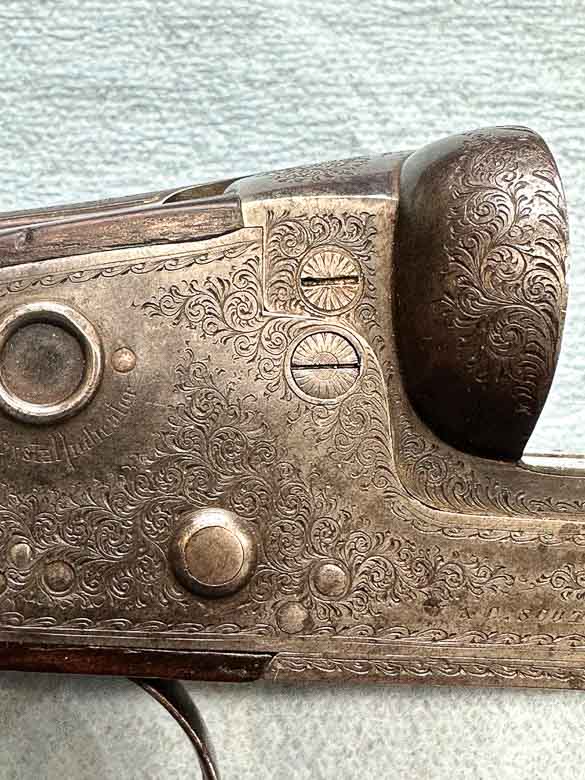
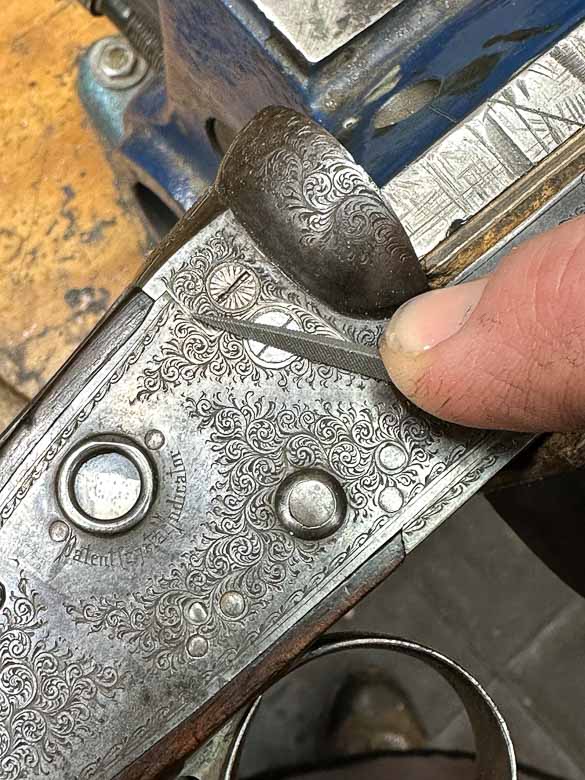
There are many instances where small, seemingly innocuous things are, in fact, of monumental importance. I am reminded of a new pair of hunting boots I acquired some years ago. The boots themselves were of the highest quality, although, as it turned out, the laces were not. Halfway through the second day of hunting in North Dakota, the savagely abrasive prairie grass completely shredded the laces, rendering my fine new boots relatively useless. At the time I was four miles from my truck, and I paid a rather uncomfortable price for my inattention to the little things.
I feel that gun screws are regarded similarly to how I regarded my boot laces. Humble screws are what literally hold our guns together, yet they are rarely considered and their importance is underappreciated.
A screw’s primary function is to create force in order to affix one thing to another and in some cases to form a physical barrier to stop movement (e.g., the ejector-retaining screws that go through the front lumps of most side-by-side barrels). When a screw is turned, be it in wood or metal, the helical teeth—properly called “threads”—convert the radial/turning force into linear force. It’s the linear force that creates the tension that holds things together. This may seem like a rather rudimentary concept, with screws being so common and ubiquitous in our lives, but this was not always the case.
Archytas of Tarentum (5th Century BC) and Archimedes (3rd Century BC) have both been credited with inventing the screw. The earliest examples were large wood screws used to press oil and juice from olives and grapes. By the 1500s in Europe, screws were being made of various metals. In 1775 British mathematician and toolmaker Jesse Ramsden invented a mechanism to accurately cut threads with a lathe, although standardization and mass production would not happen until the 1860s. The accurate manufacturing of screws allowed for technological advances in things such as measuring implements, clocks and other precision-manufacturing equipment. The reciprocal nature of these technological advances did much to fuel the Industrial Revolution. Gunmakers have always been known for their mechanical innovations and for readily using new technology—much of which has been facilitated by the humble screw.
Gun screws are predominantly made with hardened-steel cutting tools called taps and dies. Taps and dies come in matching sets. The tap is the male form of the screw and is used to cut threads into the interior of the hole that the screw turns into. The die is the female inverse of the tap and is used to cut threads into the exterior of a cylindrical rod, creating the body of the screw.
Historically, gunmakers have made their tap-and-die sets by hand. To make a set, rough threads are filed into a piece of steel rod approximating the desired screw. Two or four relief cuts, or flutes, are cut the length of the roughly shaped screw. These flutes create relief surfaces that turn the rough screw into the cutting tool, now called a tap. The rough tap is then hardened and used to make the die. To make the die, a hole is drilled in a steel plate and the rough tap is screwed all the way though the plate, cutting threads in the hole as it is turned. The hand-filed threads on this rough tap are not completely uniform. As the rough tap is turned and cuts completely through the plate, it uniformly cuts to its largest dimensions, creating uniform interior threads in the die plate. The die plate is then hardened. The rough tap is then discarded, and the new die plate with its uniform interior threads is used to make another final tap with uniform matching exterior threads. Effectively, a rough tap is used to make a uniform die, and that uniform die is used to make a matching uniform tap. These tap-and-die-plate sets were handed down generationally, and no two were alike. Sometimes master tap-and-die sets were made and used only to make the working taps and dies for manufacturing, so there could be some measure of uniformity within a given shop; but prior to the late 1860s there was a startling amount of variation.
In 1841 English inventor and entrepreneur Sir Joseph Whitworth, whose contributions to gunmaking cannot be overstated, proposed the idea that screw design and dimensions be nationally standardized. In 1861 the same idea was put forth in the US by William Sellers. For obvious reasons the idea was well accepted, and by the late 1860s most screw designs and dimensions were standardized. This meant that standardized taps and dies could be commercially manufactured. The old way of handmaking tap-and-die sets—and the variations and incompatibilities that resulted—became a thing of the past. Interestingly, it was not until 1948 that the US, Britain and Canada all agreed to the same standards. In this modern era taps and dies can be purchased from industrial-supply companies, and some of the more common sizes can be found in hardware stores.
Screws and their corresponding taps and dies are classified by their diameters and sizes of their threads. In the English system it’s diameter and threads per inch, so a ½-20 is one-half inch in diameter and 20 threads per inch. With the metric system, it goes by diameter and the width of a single thread, so an M12-1.75 would be 12mm in diameter with a single thread being 1.75mm wide. Thread size is typically proportional to the diameter of the screw, so smaller-diameter screws tend to have finer threads. Gun screws tend to have very fine threads that can range from 28 to 56 threads per inch and occasionally even finer.
Gun screws may need to be replaced for many reasons. They can be damaged by physical trauma. The threads may become corroded and seized due to poor maintenance. Often when a new stock is made, the trigger-guard screws and possibly the action screw will be replaced. The screw head or slot may have been buggered by someone using an ill-fitting screwdriver (or “turnscrew” in British parlance).
Mainly for aesthetic reasons, gun screws tend to have very thin slots, necessitating that the screwdriver blades used to turn them be similarly thin. The actual sizes of the slots will vary between makers, but they all tend to be thin compared to standard machine-screw slots. Gunsmithing screwdriver blades need to be precisely ground to fit the screws they will be used on—in many cases on a one-off basis. These screwdrivers also need to be precisely heat-treated, so that if too much force is applied, the blade will distort before the screw slot is damaged. An improperly heat-treated screwdriver blade can shatter when too much force is applied. This can cause catastrophic damage to the screw and the surrounding wood and metal.
When a fine-gun screw is damaged and must be replaced, the new screw is almost always made from scratch. Hopefully the threaded portion of the screw is not still in the hole, and if it is, hopefully it can be easily removed. If the threaded portion cannot be easily removed, it must be extracted with picks or drilled out, and great care must be taken not to damage the surrounding material. Using a micrometer and a thread-pitch gauge, the old screw is thoroughly inspected to determine its dimensions. Ideally it is a standard size and a commercially available die can be used. A piece of good-quality, high-carbon, heat-treatable steel round stock is used. The stock will be slightly larger in diameter than the largest diameter of the old screw. The round stock is chucked up in a lathe, and the body of the screw and the head are turned down to the proper diameter. The threads are then cut into the body of the screw using a die that is held by a sleeve attached to the tail stock of the lathe. The screw is not removed from the chuck until all of the machining processes are complete. This is done so that all of the diameters and thread cutting are completely concentric to each other. The threaded portion is then trimmed to length. The head of the screw is left taller than necessary, so the screwdriver slot can be cut and properly regulated. A slave slot is cut, and the screw is then turned in its corresponding threaded hole.
This is where things can get interesting and tedious. If the tap used to thread the hole was not an exact standard size or was a little worn, the threads of the new screw must be altered to fit. This might be done using a tiny triangle file, or in some cases the die itself is altered. With any gun built before WWII, there is typically some final fitting required. The new screw is then turned in with the proper amount of tension, and the final regulated slot position is marked and cut in. The slot is cut with a special fine-tooth saw with all the set ground off the teeth. The head of the screw is then filed down to the surface of the surrounding area, with great care being taken to not scratch the surface near the screw head. The screw is then removed and the head final-polished. If necessary, the head is engraved to match the original. The whole screw is then hardened and tempered for maximum strength and durability. Once heat-treated, the screw must be blackened or patinaed to match the condition of the original screw.
Gun screws come in many different shapes and sizes. A simple screw, such as a lockplate screw, can easily take five hours to make. A more complicated screw that has a tapered body, like an action screw, takes considerably longer. Some gun screws are truly tiny. For example, many lock screws and screws from the trigger mechanism can easily sit on a dime, two or three at time, and have plenty of room.
Though rarely considered, screws and their development and manufacturing are interesting and historically significant parts of gunmaking. The next time you pick up a fine gun, take the time to appreciate the humble screw.
Buy This Issue / Subscribe Now
Read our Newsletter
Stay connected to the best of wingshooting & fine guns with additional free content, special offers and promotions.